Trento is situated in the Italian Alps about an hour’s drive north of the historic violin making towns of Verona and Mantua. It’s home to a company named SMART3K, which specialises in multiscale 3D modeling of objects, including body parts for surgical use and topography of terrain (by drone). Curious about its potential application for musical instruments, I brought them a 1682 Nicolò Amati violin to be scanned to see exactly how the process worked.
SMART3K was founded at the end of 2012 as a spin-off of the Fondazione Bruno Kessler, one of Italy’s leading research institutes, and the scan itself took place at the Fondazione buildings in Trento. It’s very new technology, developed in conjunction with partner 46 Gradinord, and the process itself is highly technical, with a dash of resourcefulness – a bicycle wheel was used to regulate the rotation of the instrument, each spoke representing a different shot. To scan the Amati involved ten hours of shooting with four technicians to take over 3,600 photographs. Afterwards it took several days to adjust the images manually. Meshing color information for all 3,600 views is extraordinarily complicated. As any photographer of violins knows, it’s difficult to eliminate reflections and glare from a curved reflective surface. With a static image you can minimise this through lighting. But with 3D imaging there are too many reflections to eliminate, so they have to be masked out manually before stitching the images together.
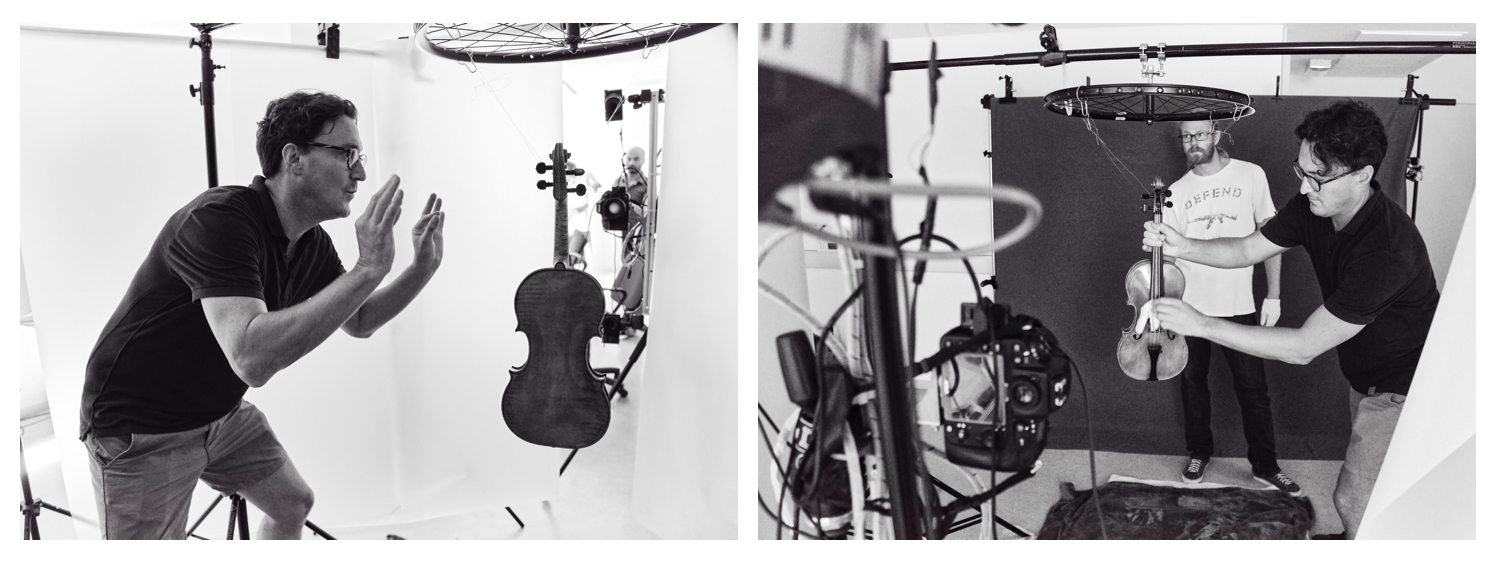
Setting up the Amati for scanning. The violin was suspended from a bicycle wheel to allow it to turn 360 degrees
The images were loaded on to a supercomputer, which spent 60 hours matching up all the pixels to create the final 3D composite. The final rendering isn’t (yet) as sharp as it could be, but the result, as shown below, is a detailed 3D image that can be rotated and zoomed in to view small details.
So far the process is too lengthy and complex for commercial application, but it has great potential implications for rendering violins and, of equal importance, for aiding restoration. Several of our colleagues are already using 3D scanning technology to make patches and corrected counterforms for restoration projects. The precision and detailing of patches generated from 3D scans allows us the most conservative means of repairing worm damage and other complicated restorations. 3D scanning and computer-generated patch routing is a minimally invasive technology that could replace the messy and dangerous gels and plaster casts that are currently used. In time it could become a vital resource for violin makers and restorers.
For further information see 3D Musical Instrument Models.